그 후에스테퍼 모터작동 전류의 역할에 대한 회전 억제가 시작될 것입니다. 이는 엘리베이터가 공중에 떠 있는 것과 같습니다. 이 전류는 모터를 가열하게 하는데, 이는 정상적인 현상입니다.
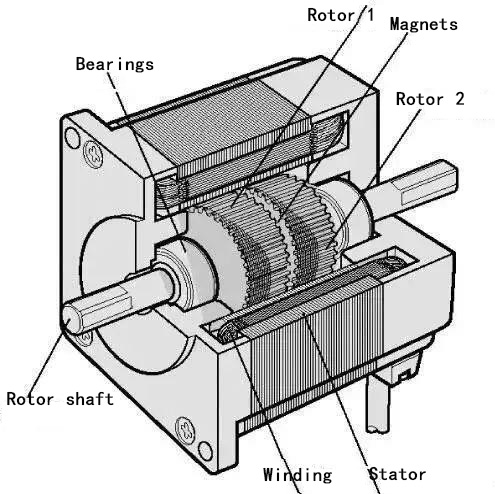
첫 번째 이유.
가장 의미 있는 장점 중 하나는스테퍼 모터는 개루프 시스템에서 달성할 수 있는 정밀 제어입니다. 개루프 제어는 (로터) 위치에 대한 피드백 정보가 필요하지 않음을 의미합니다.
이 제어 방식은 입력 스테핑 펄스만 추적하여 로터의 위치를 파악하기 때문에 광학 인코더와 같은 값비싼 센서와 피드백 장치를 사용할 필요가 없습니다. 최근 일부 고객들이 상서 모터 엔지니어들에게 스테퍼 모터도 열 문제가 발생하기 쉽다는 의견을 제시했는데, 어떻게 해결해야 할까요?
1, 줄이세요스테퍼 모터열 발생을 줄이는 것은 구리 손실과 철 손실을 줄이는 것입니다. 양방향 구리 손실을 줄이고 전기적 음과 전류를 줄이려면 모터, 즉 2상 스테퍼 모터를 사용할 때 저항이 작고 정격 전류가 가능한 한 작은 모터를 선택해야 합니다. 2상 스테퍼 모터는 병렬 모터가 아닌 직렬 모터로 사용할 수 있지만, 이는 토크와 고속 회전 요구 사항과 상충되는 경우가 많습니다.
2. 모터를 선택한 경우 드라이브의 자동 반전류 제어 기능과 오프라인 기능을 최대한 활용해야 합니다. 전자는 모터가 정지 상태일 때 자동으로 전류를 줄이고, 후자는 단순히 전류를 차단합니다.
3. 또한, 세분화된 스테퍼 모터 구동은 전류 파형이 정현파에 가깝고 고조파가 적기 때문에 모터 발열이 적습니다. 철손을 줄이는 방법은 여러 가지가 있으며, 전압 레벨이 철손과 관련이 있습니다. 고전압 구동 모터는 고속 특성을 향상시키지만 발열량도 증가합니다.
4. 고주파 대역, 부드러움 및 열, 소음 등의 지표를 고려하여 적절한 구동 모터 전압 레벨을 선택해야 합니다.
두 번째 이유.
스테퍼 모터의 열은 일반적으로 모터 수명에 영향을 미치지 않지만, 대부분의 고객은 주의를 기울일 필요가 없습니다. 하지만 심각한 악영향을 초래할 수 있습니다. 예를 들어, 스테퍼 모터의 각 부품의 내부 열팽창 계수가 구조적 응력의 변화에 따라 달라지거나 내부 공극의 미세한 변화가 스테퍼 모터의 동적 응답에 영향을 미치고, 고속에서 스텝이 쉽게 이탈될 수 있습니다. 또 다른 예로, 의료 기기나 고정밀 검사 장비처럼 스테퍼 모터의 과도한 열 발생을 허용하지 않는 경우가 있습니다. 따라서 스테퍼 모터의 열 관리가 필수적입니다. 모터 열은 이러한 요인들에 의해 발생합니다.
1, 드라이버에서 설정한 전류가 모터의 정격 전류보다 크다
2, 모터의 속도가 너무 빠르다
3. 모터 자체의 관성과 위치 토크가 크기 때문에 중속 운전 시에도 발열이 발생하지만, 모터 수명에는 영향을 미치지 않습니다. 모터의 감자 온도는 130~200℃이므로, 70~90℃의 온도는 정상적인 현상이며, 130℃ 미만이면 일반적으로 문제가 되지 않습니다. 과열이 실제로 감지되면 구동 전류를 모터 정격 전류의 약 70%로 설정하거나 모터 속도를 낮춰서 일부 낮추십시오.
세 번째 이유.
스테퍼 모터는 디지털 구동 장치로서 모션 제어 시스템에 널리 사용되고 있습니다. 스테퍼 모터를 사용하는 많은 사용자와 관련자들은 모터가 높은 열을 발생시킨다고 생각하지만, 이것이 정상적인 현상인지 확신하지 못하고 있습니다. 실제로 열은 스테퍼 모터에서 흔히 발생하는 현상이지만, 어느 정도의 열이 정상으로 간주될 수 있을까요? 그리고 스테퍼 모터의 열을 최소화하는 방법은 무엇일까요?
다음은 실제 응용 프로그램에서 실제 작업에 도움이 되기를 바라며 몇 가지 간단한 분류를 수행해 보겠습니다.
1 모터 가열 원리
우리는 일반적으로 모든 종류의 모터, 내부 코어 및 권선 코일을 봅니다. 권선에는 저항이 있으며 전원이 공급되면 손실이 발생합니다. 손실의 크기와 저항 및 전류의 제곱은 손실에 비례합니다. 이를 구리 손실이라고 합니다. 전류가 표준 DC 또는 사인파가 아닌 경우 고조파 손실이 발생합니다. 코어에는 히스테리시스 와전류 효과가 있으며 교류 자기장에서도 손실이 발생하며 재료의 크기, 전류, 주파수, 전압에 따라 달라지며 이를 철손이라고 합니다. 구리 손실과 철손은 열의 형태로 나타나 모터의 효율에 영향을 미칩니다. 스테퍼 모터는 일반적으로 위치 정확도와 토크 출력을 추구하지만 효율이 상대적으로 낮고 전류가 일반적으로 비교적 크며 고조파 성분이 높습니다. 전류 교류 주파수도 속도에 따라 변하기 때문에 스테퍼 모터는 일반적으로 열이 발생하며 일반적인 AC 모터보다 상황이 더 심각합니다.
2 스테퍼 모터 열 적정 범위
모터의 열 발생 허용 범위는 모터의 내부 절연 수준에 따라 크게 달라집니다. 내부 절연은 고온(130도 이상)에서만 파괴됩니다. 따라서 내부 온도가 130도를 넘지 않는 한 모터는 링을 손상시키지 않으며, 표면 온도는 90도 미만이 됩니다. 따라서 스테퍼 모터의 표면 온도는 70~80도가 정상입니다. 간단한 온도 측정 방법은 온도계를 사용하면 대략 다음과 같이 확인할 수 있습니다. 손으로 1~2초 이상 만져도 60도를 넘지 않습니다. 손으로 만져도 70~80도 정도입니다. 물 몇 방울이 빠르게 증발하면 90도가 넘습니다.
속도 변경이 가능한 3단계 모터 가열
정전류 구동 기술을 사용하면 스테퍼 모터가 정지 상태 및 저속에서 전류가 일정하게 유지되어 일정한 토크 출력을 유지합니다. 속도가 일정 수준 이상 높아지면 모터 내부 역전위가 상승하여 전류가 점차 감소하고 토크도 감소합니다. 따라서 구리 손실로 인한 발열은 속도에 따라 달라집니다. 정지 상태 및 저속에서는 일반적으로 높은 열이 발생하는 반면, 고속에서는 낮은 열이 발생합니다. 그러나 철손(비중은 적지만)의 변화는 동일하지 않으며, 전체 모터 열은 두 가지 열의 합으로 발생하므로 위의 내용은 일반적인 상황일 뿐입니다.
4 충격으로 인한 열
모터 열은 일반적으로 모터 수명에 영향을 미치지 않지만, 대부분의 고객은 주의를 기울일 필요가 없습니다. 하지만 심각한 악영향을 초래할 수 있습니다. 예를 들어, 모터 내부 부품의 열팽창 계수 차이로 인해 구조 응력이 변하거나 내부 공극의 미세한 변화가 발생하여 모터의 동적 응답에 영향을 미치고, 고속 회전 시 속도가 느려질 수 있습니다. 또한, 의료 장비나 고정밀 검사 장비처럼 모터의 과도한 열이 허용되지 않는 경우도 있습니다. 따라서 모터의 열 발생은 필요에 따라 제어되어야 합니다.
5 모터의 열을 줄이는 방법
발열 감소는 구리 손실과 철손을 줄이는 것입니다. 양방향 구리 손실을 줄이고 저항과 전류를 줄이려면 모터, 즉 2상 모터를 병렬 없이 직렬로 사용할 수 있는 경우 저항과 정격 전류를 가능한 한 작게 선택해야 합니다. 하지만 이는 토크와 고속 회전 요구 사항과 상충되는 경우가 많습니다. 선택된 모터의 경우, 드라이브의 자동 반전류 제어 기능과 오프라인 기능을 최대한 활용해야 합니다. 전자는 모터 정지 시 전류를 자동으로 감소시키고, 후자는 전류를 차단합니다. 또한, 분할 드라이브는 전류 파형이 정현파에 가깝고 고조파가 적기 때문에 모터 발열도 줄어듭니다. 철손을 줄이는 방법은 많지 않으며, 전압 레벨도 이에 영향을 미칩니다. 고전압으로 구동되는 모터는 고속 특성이 향상되지만 발열도 증가합니다. 따라서 고속 회전, 평활도, 발열, 소음 등의 특성을 고려하여 적절한 드라이브 전압 레벨을 선택해야 합니다.
모든 종류의 스테퍼 모터는 내부가 철심과 권선 코일로 구성됩니다. 권선에는 저항이 있으며, 통전 시 손실이 발생합니다. 손실의 크기는 저항과 전류의 제곱에 비례하며, 이를 구리 손실이라고 합니다. 전류가 표준 직류 또는 사인파가 아닌 경우 고조파 손실이 발생합니다. 철심에는 히스테리시스 와전류 효과가 있으며, 교류 자기장 내에서도 손실이 발생하는데, 이는 재료의 크기, 전류, 주파수, 전압에 따라 달라지며, 이를 철손이라고 합니다. 구리 손실과 철손은 열의 형태로 나타나 모터의 효율에 영향을 미칩니다. 스테퍼 모터는 일반적으로 위치 정확도와 토크 출력을 중시하지만, 효율은 상대적으로 낮고 전류는 일반적으로 크며 고조파 성분이 높습니다. 전류 교류 주파수는 속도에 따라 변동하기 때문에 스테퍼 모터는 일반적으로 열이 발생하며, 일반적인 AC 모터보다 상황이 더 심각합니다.
게시 시간: 2022년 11월 16일